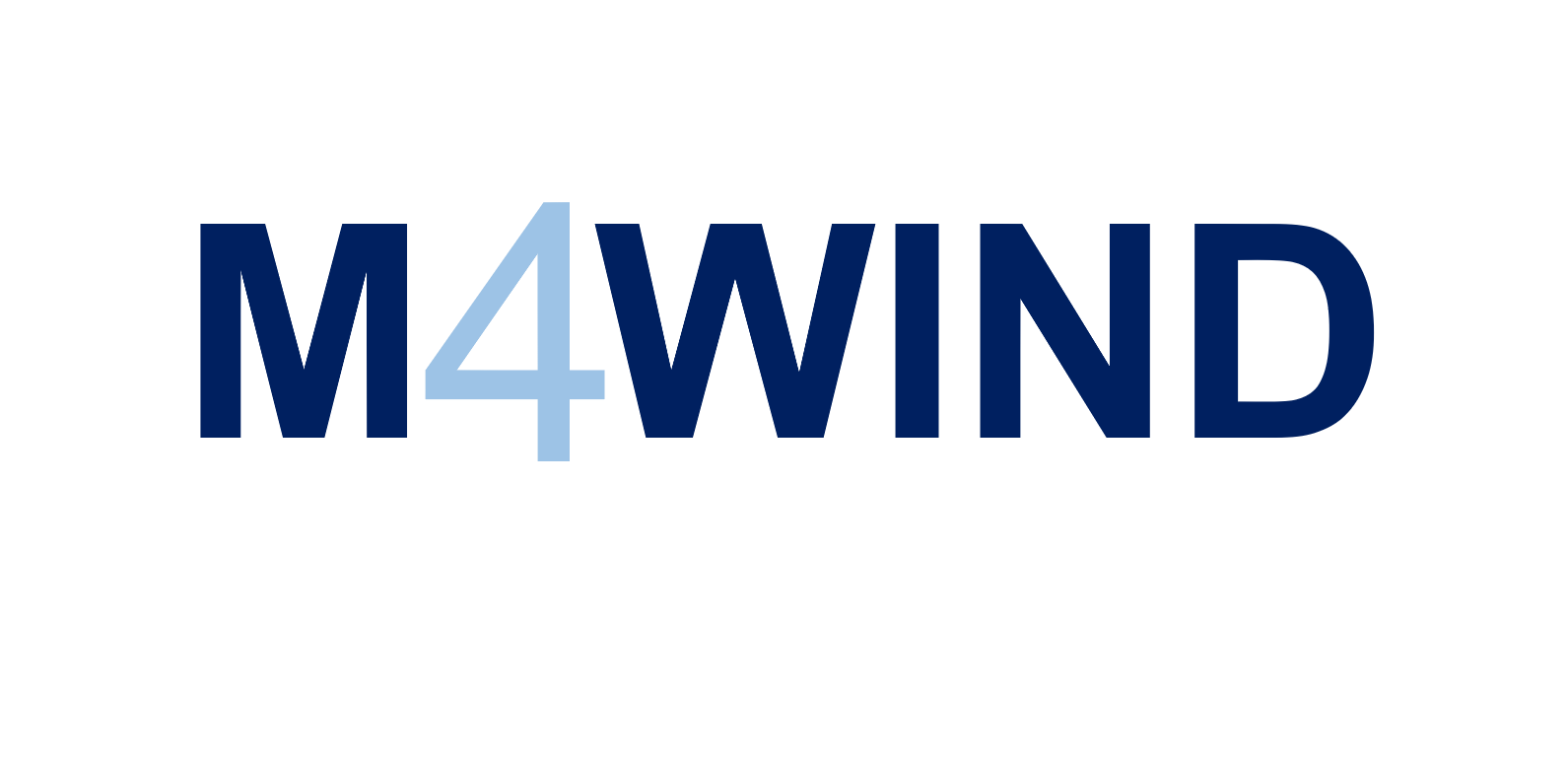
M4WIND – Monitoring, Modelling and Machine learning for Managing the operating life of WIND farms
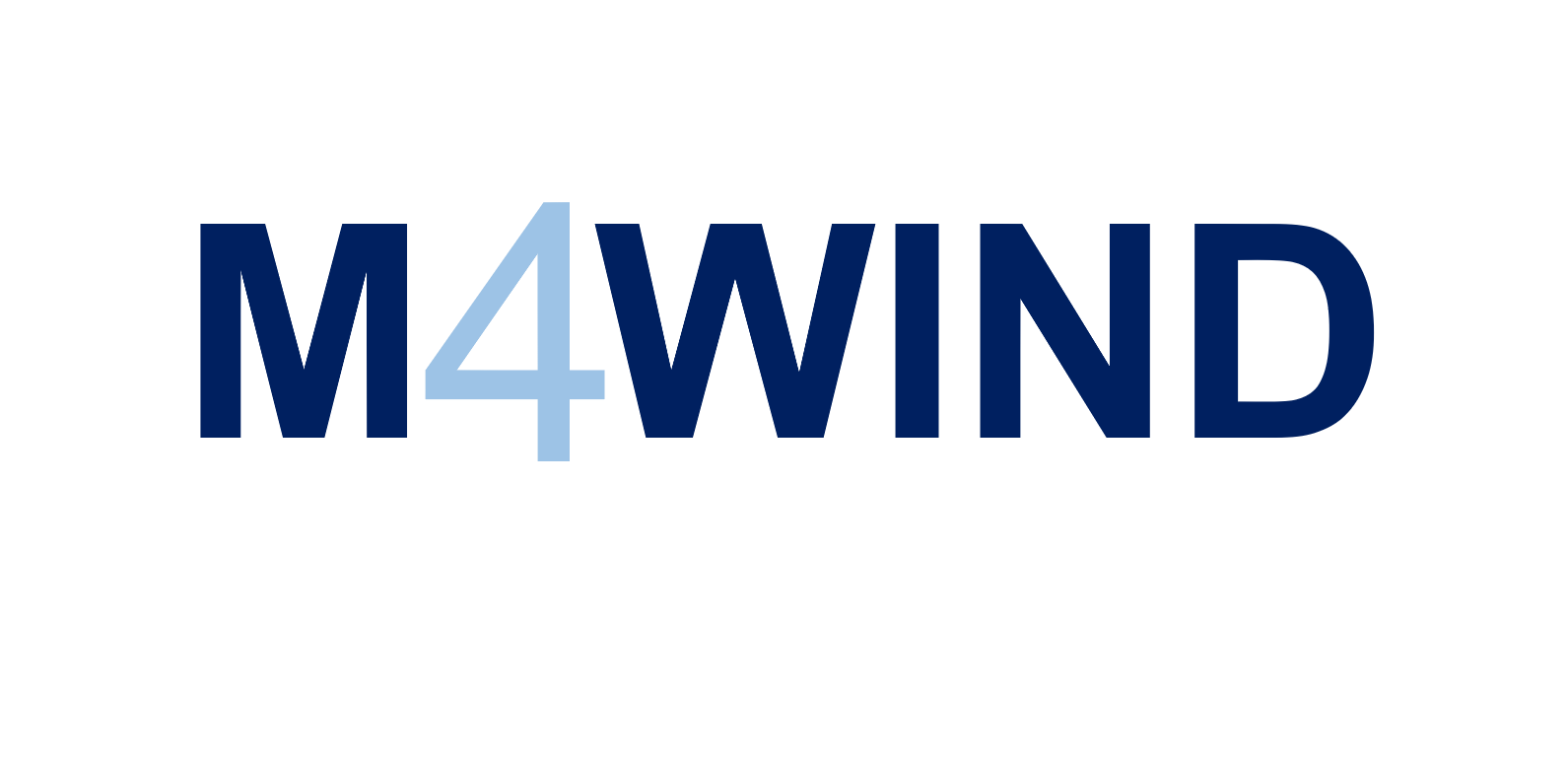
Project name: M4WIND – Monitoring, Modelling and Machine learning for Managing the operating life of WIND farms
Project code: M4WIND
Project timeline: 2023 - 2026
Research group: Mechanical Design
Objective
This Project is lead by Faculdade de Engenharia do Porto, IDMEC is the research partner and Ventient Energy is the industrial partner. In the context of fatigue analyses, an important source of uncertainties in the design phase of modern WT (with large rotors that might be supported by floating platforms) and in the evaluation of consumed fatigue life of older models comes from the difficulty of estimating the realistic stress time histories in the critical sections, since these are influenced by complex load scenarios, by the control algorithms of the WTs and by their aerodynamic, (hydrodynamic) and structural behaviour. Considering this background and the available research infrastructure, the major goals of the project are the accurate characterization of past, present and future fatigue stresses (or fatigue consumption indexes) on tower and blade sections and the development of tools to enable a smart management of the operating life of these critical structural components. The foremost novelty of this application is the combined use of 3 Major tools: M1 ? Monitoring ? the project team has a large experience in structural monitoring of WT, unique data-bases of experimental data (ongoing monitoring projects on 7 onshore WT and on one of the largest floating WT) and innovative ideas for the development of customised monitoring devices, not only to characterise stresses but also to monitor variables that can early detect malfunctions with impact on fatigue loads. So, this will be the solid base for the methodology development and validation. M2 ? Modelling ? since measuring all relevant quantities on site is economically prohibitive, the development of digital twins calibrated with measurements is crucial to support the extrapolation of the structural responses to other (non-observed) operating scenarios and to non-instrumented sections. These will be also fundamental to support the creation of surrogate models that can simplistically model the impact of operation anomalies (such as foundation problems, rotor imbalances and yaw misalignments) on fatigue load spectra. M3 ? Machine Learning ? this includes the development of several black-box models to convert limited monitoring time-histories into parameters for fatigue evaluation of full structural elements, but also interpretable hybrid models that combine monitoring data with numerical models. Advanced machine learning models will also enable handling large populations of WT and assess the fatigue of fleets using selected more instrumented WT. The 3Ms will allow estimating the consumed fatigue life of full wind farms with minimal instrumentation, accurately quantify the impact of key factors on fatigue loads and open the path for the fourth M, the Management of the operating life. In this topic, the ambition of the project team is the creation of procedures to influence the future rate of fatigue consumption of the WTs of a specific wind farm, with manipulations on the WTs control system (rotor torque and blades pitch laws as a function of wind characteristics, namely speed, turbulence and direction).